Fibox uses modern CNC machinery designed and built specifically to machine plastic electrical enclosures with holes, cutouts, and recess with pinpoint accuracy.
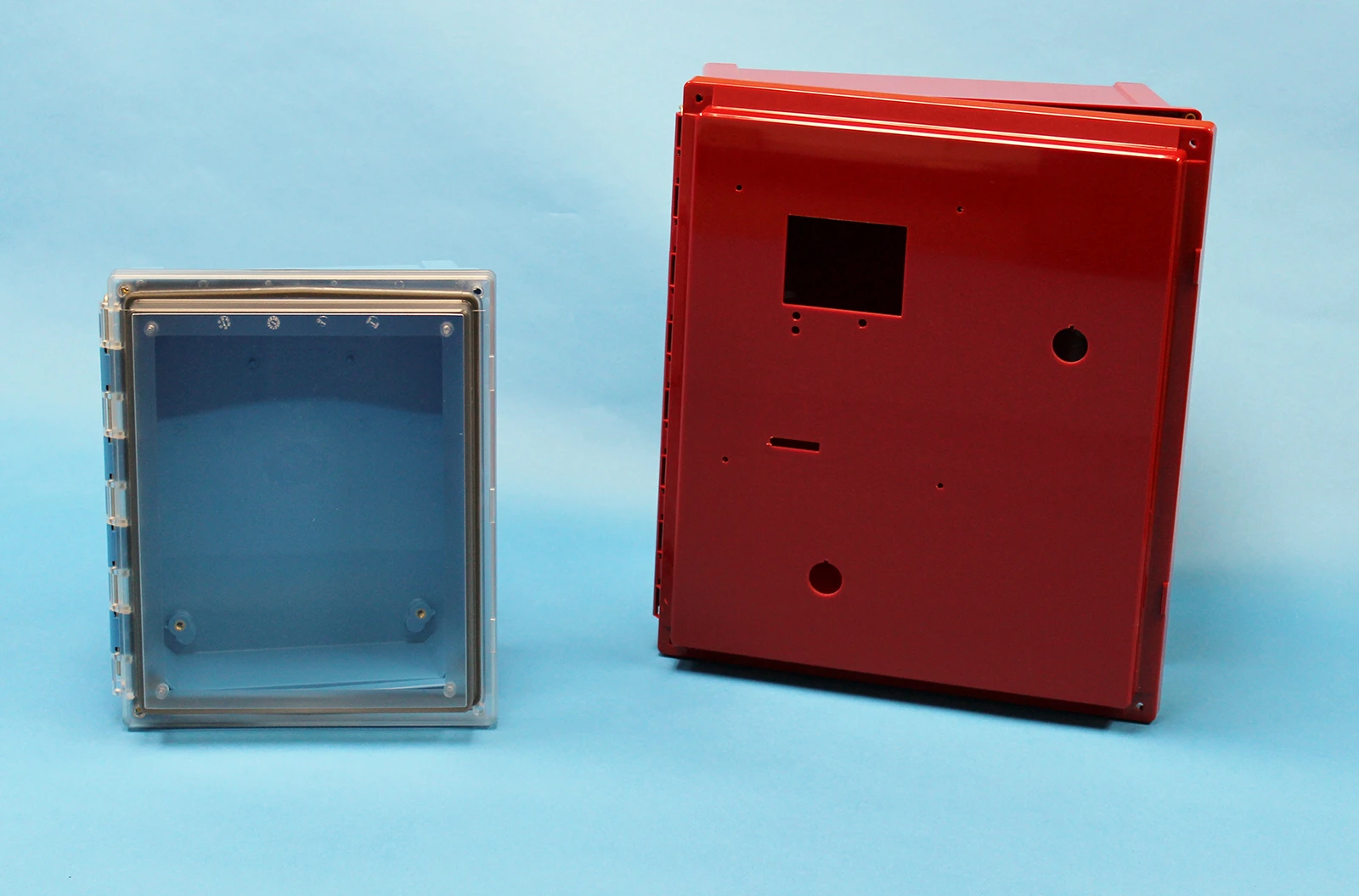
Now more than ever, non-metallic enclosures offer cost-effective value for customized electronics packaging. Specialized CNC machines permit enclosure manufacturers to offer extensive customization or modification services at lower prices and faster turnaround times. When the volume takes off, plastic permits easy ramp-up by substituting customized molding for CNC customization; with a basic understanding of the process and the input required, the design engineer can now obtain the most cost-effective solution for all ranges of piece part volume.
Download Fibox's CNC Machning Brochure.
Customization Impact on Enclosure Selection
Enclosure size, the operating environment, and the NEMA rating make up the main criteria for selecting an enclosure. Within Fibox’s wide range of products, you may find even more than one enclosure choice, or you may narrow your selection based on your required features. For example, a cable gland may be needed for wire entry. If a threaded mounting hole is required, a thin wall enclosure may not be suitable for threading, and a thicker wall (e.g., 3 mm) enclosure should be selected.
If you are unsure of your enclosure selection or the impact of desired modifications, please contact our application staff. Fibox can guide your enclosure selection while suggesting cost-effective customization methods.
Factors Impacting Cost
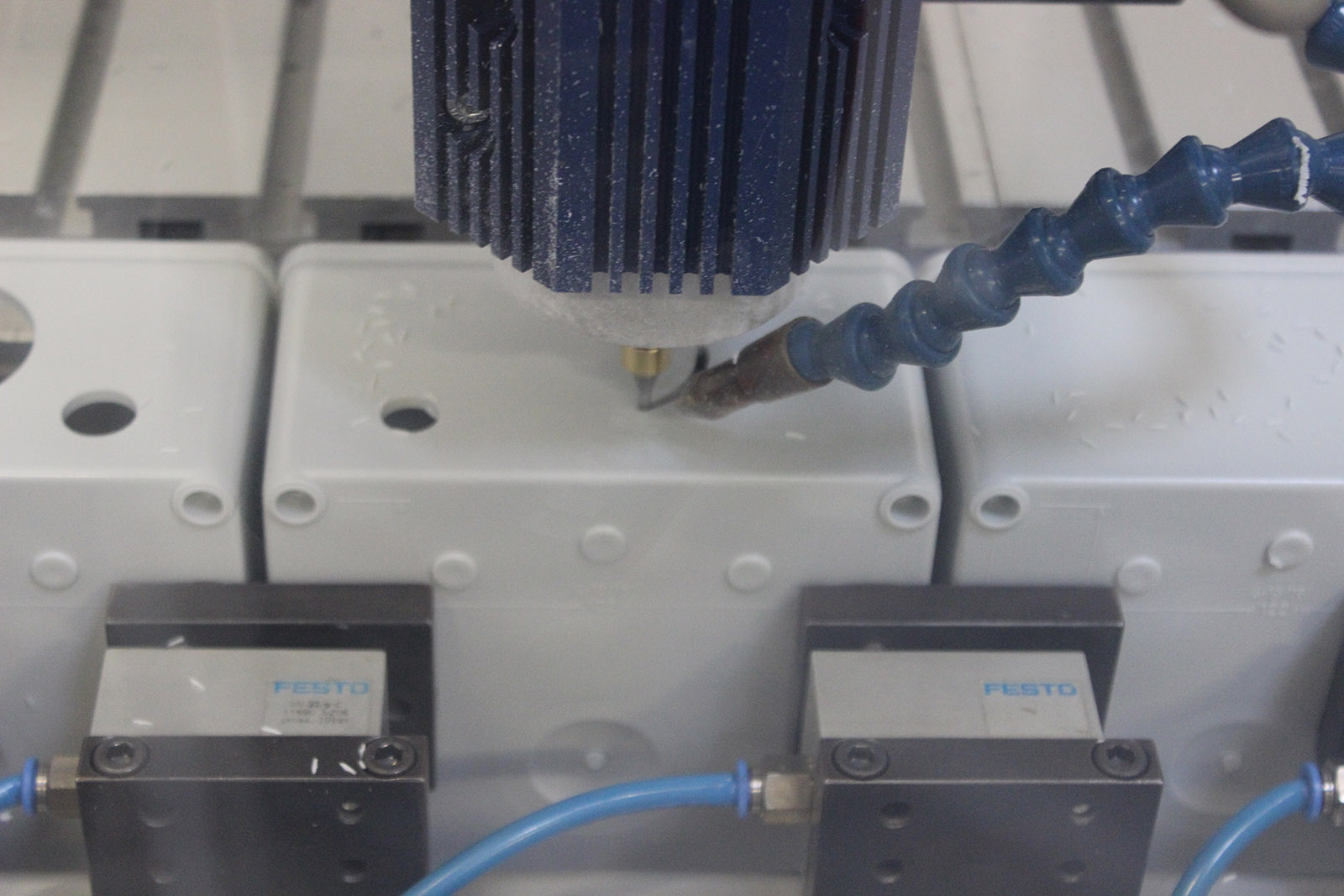
After the enclosure, many items can affect cost. From the beginning design phase, Fibox will work with you to advise how to reduce costs. There may be a one-time engineering charge to review the design and to program our CNC machinery. Usually, there is a cost required to set up the CNC machine, which is a recurring cost with each machining run of enclosures. Of course, the actual modifications also affect cost. A large cutout for a DIN meter is typically more expensive than a small round hole. A milled recess is more costly than an open slot. The total time to machine the modification determines the cost.
One of the more significant cost drivers is the number of enclosure sides modified because each side requires separate plotting, and each side requires set-up. For example, two holes on each of the two sides will be more costly than four holes on one side. The cover, lid, or door is a separate part, requiring an independent set-up and program. The designer can control costs by understanding that different machining operations may require various tools.
Tool changes, even when automatically done, require time, affecting throughput. And, more time equals more money. In many cases, a simple design change can minimize tool changes. For example, does that cutout corner radius need to be 1 mm, or can it be 1.5 mm? Fibox personnel will review your design and offer suggestions to reduce cost. Tight tolerances are achievable in machining holes and hole pattern relationships, but specifying excessively tight tolerances will increase costs. The repeatability of machined patterns, unit to unit, is excellent, but plastic’s nature means that overall enclosure dimensions may change slightly due to molding process variations. Dimensionless to piece part center lines and mold parting lines minimizes these variations’ impact on the overall cost. Fibox staff is ready to assist with your specification.
Documenting the Design
Ideally, the designer should provide Fibox with a computer-aided design (CAD) file indicating the modifications. Fibox provides CAD files of their enclosures, and the designer should use these as their starting point. CAD files ensure dimensional accuracy and simplify drawing interpretation. While a CAD file is ideal, Fibox can work with just about anything. However, additional drawing costs may result. Using Fibox’s CAD files during your design will speed the process and lower your overall costs.
To request more information on Fibox customized enclosures, contact us today.